Rubber Roofing
Rubber Roofing
Our team of experienced professionals will work with you to install any type of rubber roofing system on your property, whether it’s a new or existing structure.
Contact Us Immediately
Rubber roofing is appropriate for harsh environments and provides you with one of the most reliable and durable roofs available, often lasting between 30 and 50 years. A felt flat roof may over time accumulate moss and algae, but since synthetic rubber doesn’t encourage the growth of moss, your roof will always be pristine.
Do you know which material is appropriate for your needs whether you’re preparing for a new building project or need to replace a damaged roof? The three different varieties of rubber roofing—EPDM, TPO, and PVC—are long-lasting solutions with numerous advantages you might not have thought about.
EPDM Roofing
For several reasons, EPDM, a long-lasting, waterproof, elastomeric, and extremely flexible synthetic rubber, is an excellent choice for use as a single-ply roofing material. The name “ethylene propylene diene monomer,” which is the full chemical name of EPDM rubber, is what is abbreviated as “EPDM”.
Single-ply low-slope roof systems that use EPDM rubber sheets linked together to create a watertight roof membrane are referred to as “EPDM roofing.”
Almost always, when people refer to “rubber” roofs, they are referring to EPDM. Currently, the only material that can be classified as rubber and used to build whole roof systems is EPDM.
Rubber roof membranes are among the simplest to repair, despite the fact that non-reinforced EPDM tends to be easily pierced (by casual foot traffic or lost tools, for instance). EPDM roofing is renowned for being hail-resistant. Simple repairs on an EPDM roof should be doable even for those without any prior roofing knowledge.
Different EPDM Roof System Types
Single-ply roof systems are often classified according to how they are fastened to the building: ballasted, fully-adhered, and mechanically-attached systems.
Ballasted System
EPDM roofing systems that are ballasted are held in place by the weight of concrete pavers or river-washed stone (without sharp edges). The ballast is installed on top of the EPDM membrane, and the insulation and roof membrane are loose-laid over the roof deck.
In ballasted systems, the roof system is not fastened to the roof deck by fasteners or adhesives.
The rigid insulation cover board that other systems utilise to offer impact resistance is typically absent from ballasted systems. Impact resistance is provided by the ballast itself.
Ballasted EPDM roofing is consequently far more prone to punctures from foot activity than other systems because the ballast stone ages and develops sharp edges that careless footfall can force down into the soft insulation beneath the membrane.
Fully-Adhered System
The entire roof membrane of fully-adhered EPDM roofing systems is fastened to the underside of the insulation or the insulation cover board with adhesive. The metal roof deck beneath the insulation and cover board is normally secured with specialist roofing screws.
If the roof deck is made of structural concrete, adhesive may be used in place of fasteners to hold the roof system’s layers together.
All EPDM roof systems normally employ some adhesive; hence this system is referred to as “fully-adhered” rather than just “adhered” (at the field seams and at perimeter and penetration flashings).
Mechanically-Attached System
Long plastic or metal batten strips are used in mechanically fastened EPDM roofing systems to hold the membrane in place. On top of the EPDM membrane, these battens are positioned across the roof, typically at the borders of the individual sheets of EPDM that make up the field membrane.
Once the battens are in position, fasteners are screwed through them, down through the roof system, and into the roof deck. The battens already have fastener holes pre-drilled into them.
EPDM pros
- When it comes to flat or low-pitched roofs, EPDM often has the lowest cost per square foot.
- EPDM typically has a lifespan of more than 20 years.
- It can be an extremely energy-efficient roof option because it pairs well with polyiso insulation, especially if purchased in white.
EPDM Cons
- In the improper setting and when it is almost completely worn down, EPDM can be fragile.
- Ballasted EPDM systems are reasonably priced in comparison to other systems, however mechanical or fully-adherent systems are slightly more expensive than TPO.
- The black flat EPDM roofs are not often believed to be the most attractive sight.
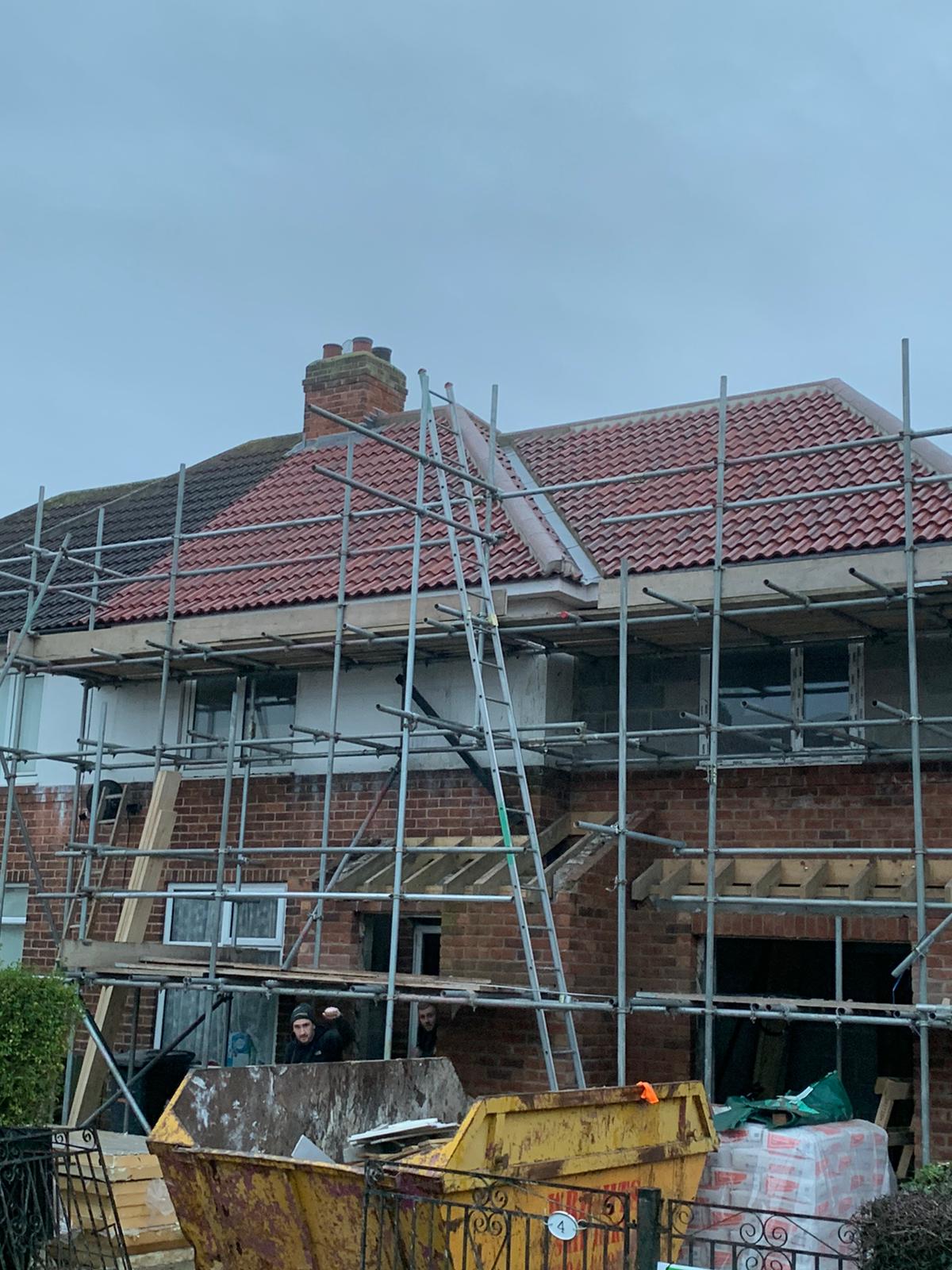
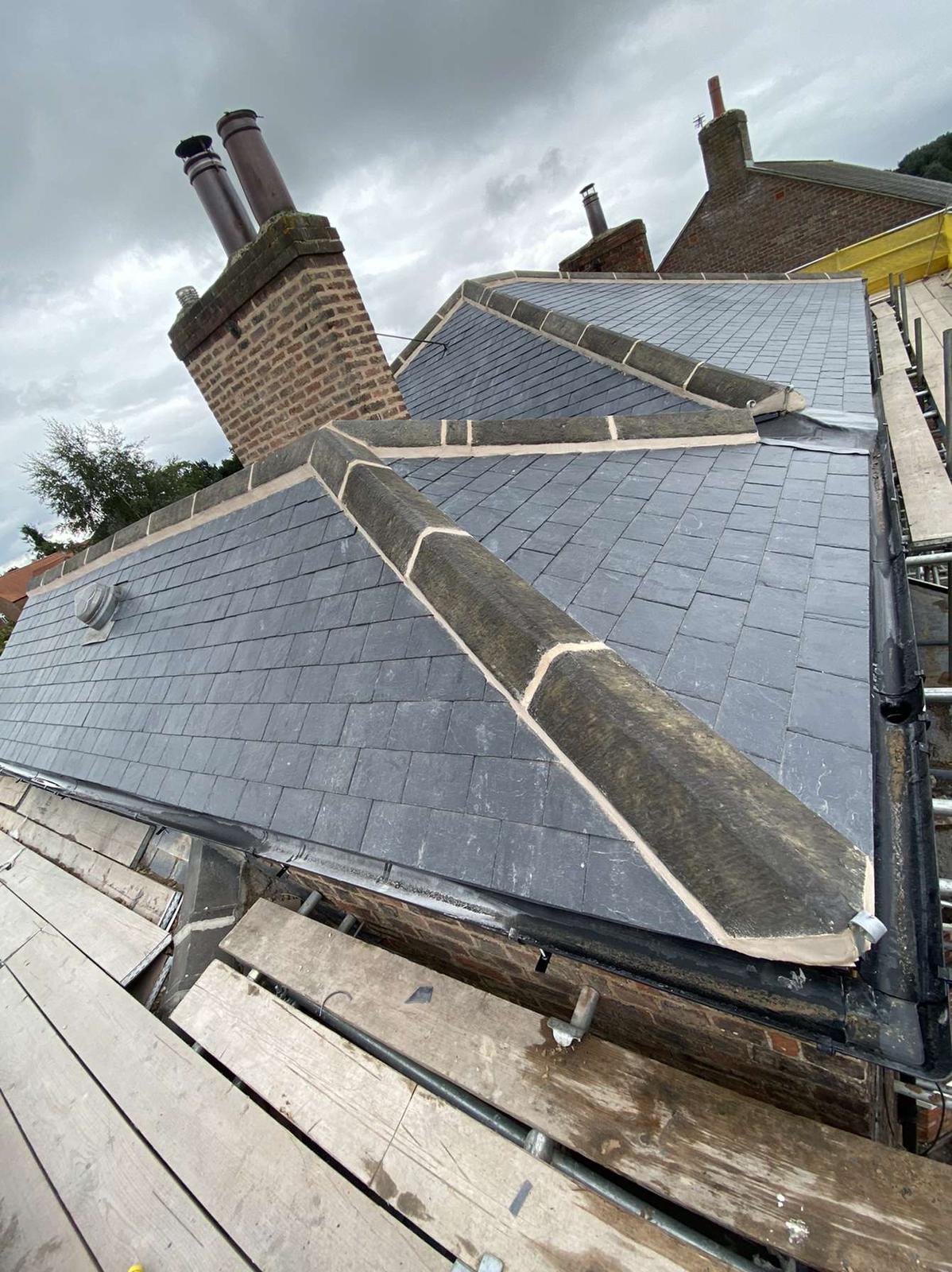
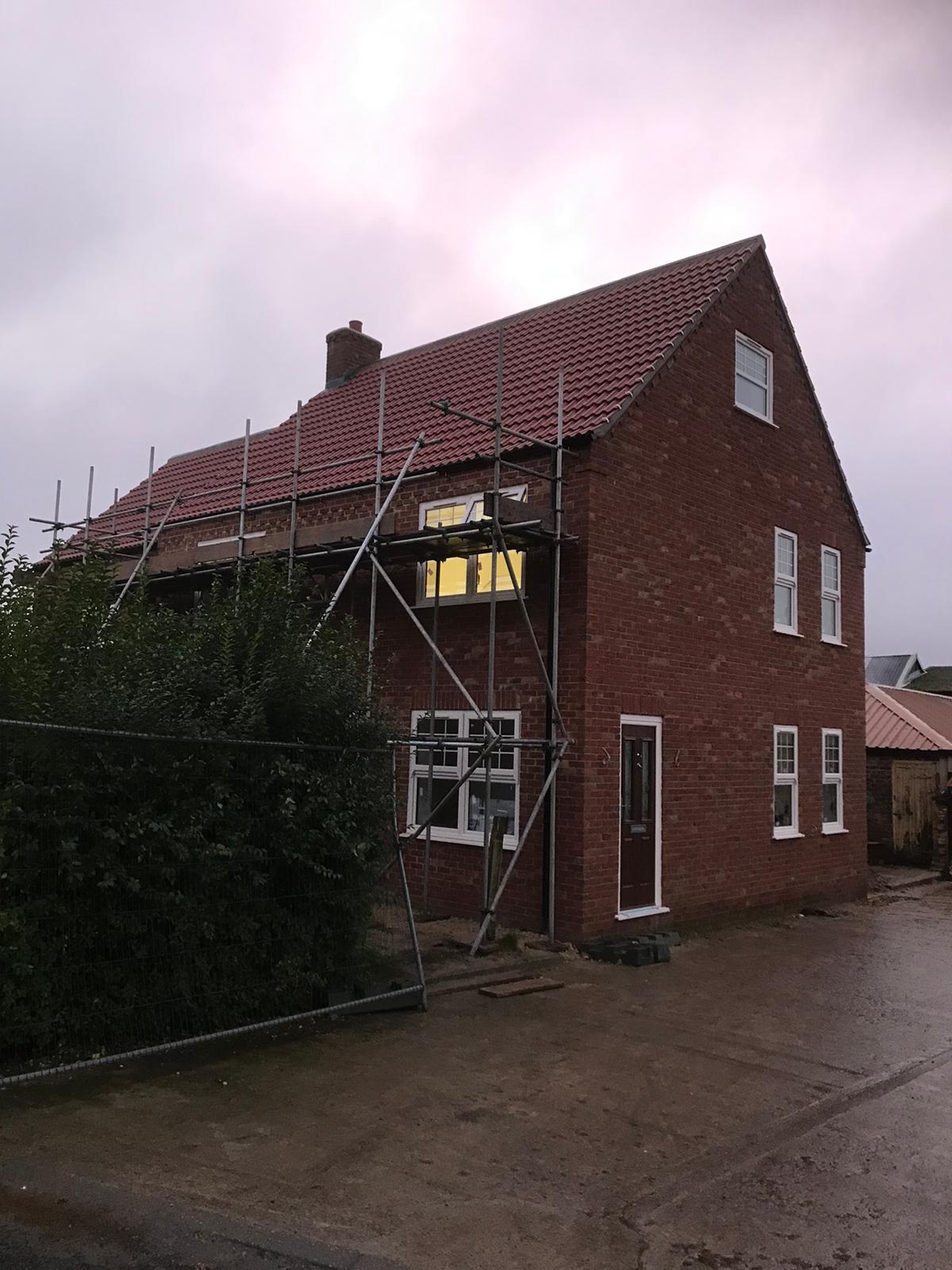
TPO Roofing
Thermoplastic Polyolefin, or TPO, is arguably the fastest-growing commercial roofing system on the market today. It may be used to cover flat and semi-flat roofs because it is constructed of a single layer of synthetic materials and reinforcing scrim. The term is a little misleading because TPO is a form of rubber, typically a mixture of polypropylene and ethylene-propylene rubber, not plastic.
TPO’s key benefit is that, compared to EPDM and other varieties of rolled rubber roofing, it often has the lowest material cost for single ply membrane roofs. The colour is the next benefit to mention. TPO is frequently white on top, which can reflect sunlight and prevent heat accumulation within buildings.
TPO membrane also has the advantage of offering a variety of installation options. It can be secured to the roof deck directly or with adhesives. In areas near chimneys and other protrusions, it can also be heat welded. See our blog post on hand welding a TPO seam for more information.
Finally, TPO is corrosion-resistant and degrades when it comes into touch with various substances. Additionally, it does not encourage the growth of mildew or algae and does not demand pressure cleaning. These characteristics make the material more simple to maintain throughout the yearly examination.
TPO Pros
- Offers exceptional protection against ozone, UV light, and some chemical exposure at a reasonable price.
- Better than EPDM at reflecting heat radiation.
- Resists fungus development, dirt buildup, tears, collisions, and punctures.
TPO Cons
- A very high-quality installation is necessary for the heat-welded seams to endure over time.
- Some versions could not endure very long after ten years.
- Technology that is more recent lacks a track record of success.
PVC Roofing
Another single-ply membrane roofing material used on flat and semi-flat commercial buildings is PVC, which stands for polyvinyl chloride. Compared to TPO or EPDM, it contains less oil and petroleum in its construction.
PVC is surprisingly robust, as seen by its breaking strength, which is at least 2413kPa, much exceeding the 1378kPa minimum breaking strength needed by ASTM.
In contrast to other membranes that require adhesive or employ a taped seam, PVC can be put by heat welding the seams together. With this type of installation, a PVC roof can change size along with a building. PVC can also be adhered to metal flashing and other parts with adhesives and sealed using solvent welding.
PVC Cons
- Strength: These roofs are capable of lasting 20 years or more.
- Chemical and fire resistance – Some commercial structures, such as warehouses and manufacturing plants, will be exposed to chemicals on a regular basis. Additionally, PVC roofs do not support combustion, burn slowly, are challenging to light on fire, and even put out a fire if the source is taken away.
- Recyclable and environmentally friendly – It reflects sunlight and reduces the heat island effect in cities. It is also very effective at heating and cooling. Oh, and even after years of use, it is recyclable.
PVC Cons
- Cost: Despite the advantages of PVC roofing, each of these qualities has a price. It often costs more per square foot than TPO and EPDM together.
- Installation – If you are replacing the roof, you must entirely remove the old one before beginning the replacement. This increases the expense of the project because removing the old roof can be highly labour-intensive.
- In cold climes, PVC roofing systems often don’t function as well. PVC becomes fragile when it becomes too cold and is susceptible to breaking if stepped on.
Installation of a Rubber Roof
Installing a rubber roof is significantly simpler and faster than installing an asphalt or slate roof. Rubber roofing on a seamless roll is typically the most economical and energy-efficient option. There are no seams underneath, thus there is a very little chance that it will leak or split. Shingles are more expensive than rolls and require nailing, much like regular shingles do. But rubber shingles are significantly lighter than slate or asphalt shingles, making them simpler to carry and install.
The current roofing is stripped down to the plywood base before applying the new roofing. Using a roll, your roof’s shape is measured and the roll is cut to fit, leaving room for chimneys, vents, etc.
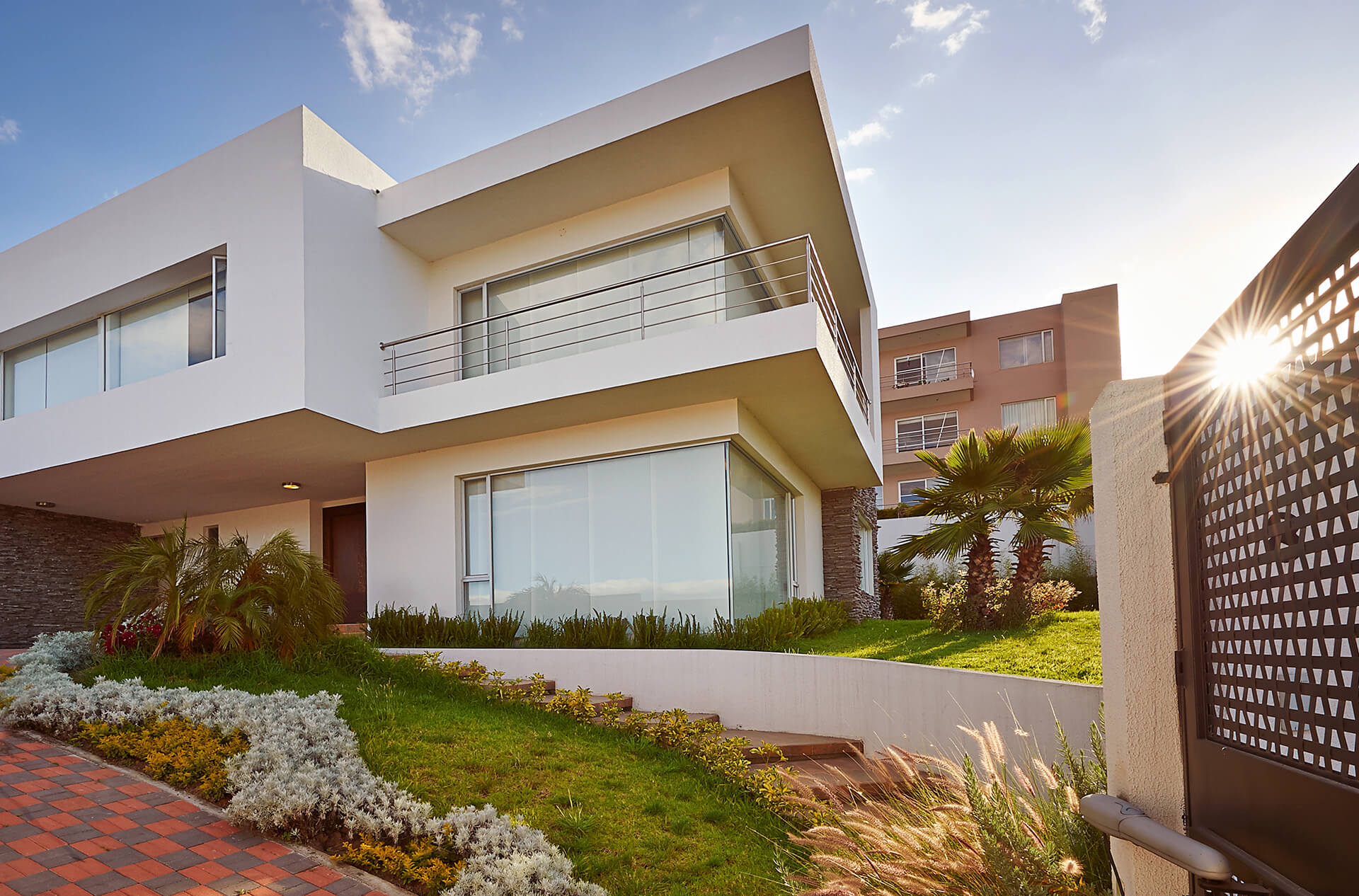
Next, any dirt and debris is swept off your roof, glue is applied, and the roll is properly positioned across your roof. It is made sure to look underneath for air bubbles. Shingles are applied in rows, just like you would with asphalt shingles.
On occasion, old shingles are covered with rubber roofing, with a layer of foam insulation in between. After that, the rubber roofing acts as a waterproof membrane. This can help you save time and money on labour while also keeping your home cooler by reflecting heat from the sun away from the roof. But keep in mind that manufacturers frequently won’t honour your guarantee if you don’t first strip your roof down to the bare minimum.
Rubber Roof Repair
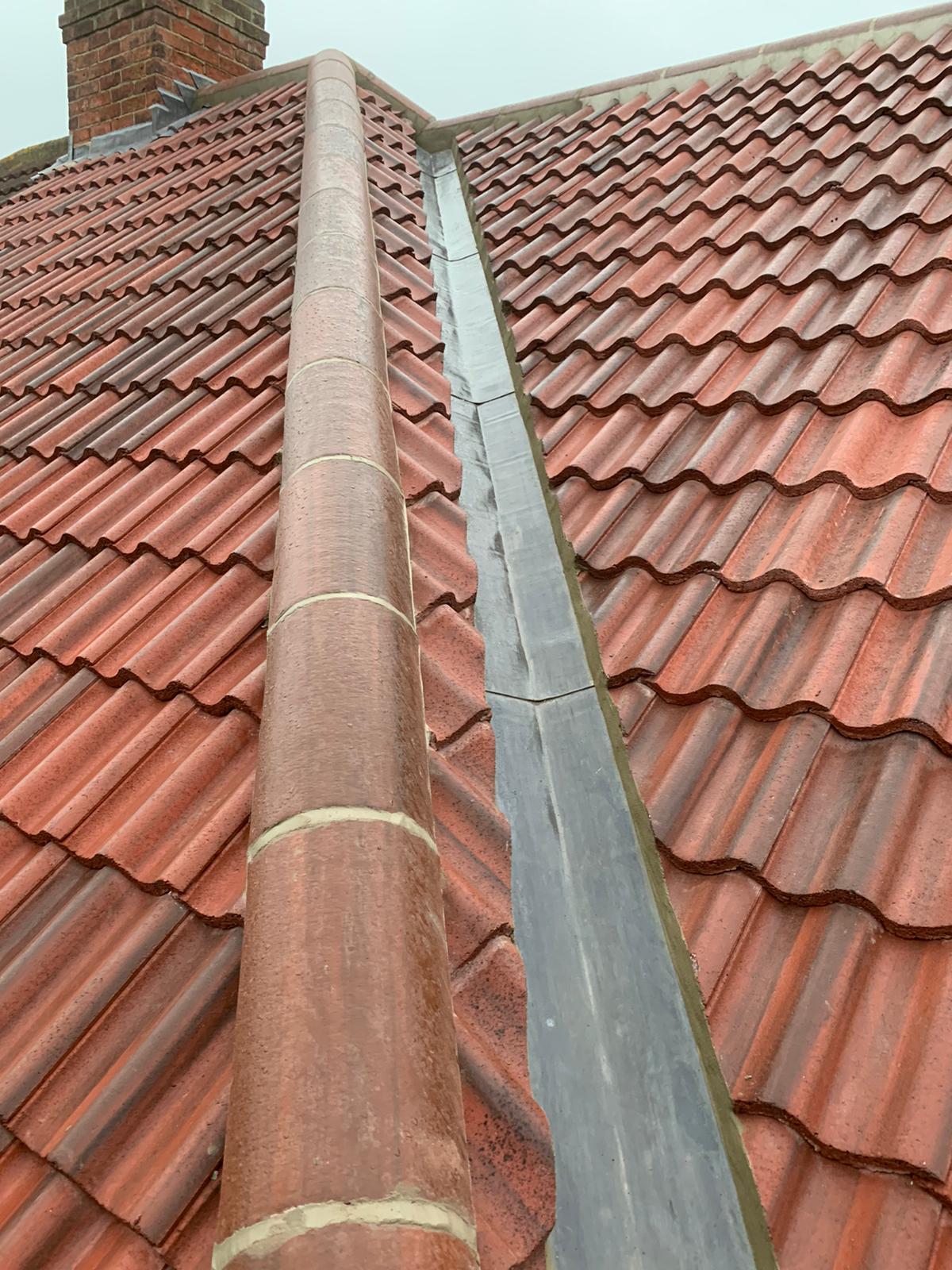
EPDM roofs are rubber-like materials that protect against UV rays, water damage, and other weathering elements such as hail. EPDM Roofs typically require repairs due to colour fading over time, as well as cracks in the material where ice can build up during the winter months, resulting in more cracking on the surface of your EPDM Roof after the spring thaw.
Problems with EPDM Rubber Roofing
Moisture and leaks
For rubber roofs that haven’t been properly maintained, leaks can be a serious issue, especially during times of severe rain. Rubber made of EPDM is waterproof and should keep your house safe from the elements. However, leaks might still happen during rainy seasons if you had poor installation or insufficient upkeep. When you notice a leak, it’s crucial to locate the cause and call a specialist to examine and fix your roof. While a temporary DIY fix might be effective, it’s crucial to have the roof fixed by a qualified professional else the issue could get worse.
Puddles of liquid
Puddles of water accumulating on your roof are another typical entry point for EPDM rubber roofing issues. Your flat roof will be level when it is first put, but with time, houses might shift, which may cause changes in the structure of the roof.
This may cause water to begin to collect on your flat roof. EPDM rubber that has been fitted correctly ought to be able to resist water without absorbing any of it, but it’s still crucial to drain any puddles as soon as you notice them. Finding any problematic pooling spots on the roof will be made easier with routine maintenance and inspections.
Shrinkage
While many EPDM rubber roofing issues are related to water, shrinking is another problem you could run into. Poor installation, an old, poorly maintained roof, and exposure to direct sunlight can all contribute to this. The flashings may be pulled from the side by a shrinking roof, causing surface splits and fissures. Leaking may eventually result from this. Your flashing can be replaced by roofing specialists, and a quality installation can stop any potential problems in the future.
How to Repair an EPDM Roof
Installing a rubber sealant like silicone to help expand out these areas where water has been getting into pieces of insulation materials as well as other places where water damage could have occurred due to leaks with the rubber sealant is the best solution for repairing this type of material if you don’t want to replace your entire roofing system yet again.
Roof leaks, holes that develop in the roofing material as a result of hail damage or other sources are some of the issues that can occur with EPDM roofs. Because of age and wear, the rubber membrane can be replaced with new materials as long as there is enough coverage for water to flow off this type of shingle roof instead of seeping into the home’s interior.
Frequently Asked Questions
A Rubber Roof Should Last How Long?
Because an EPDM rubber roof is made of rubber, it is impervious to the sun’s UV and UVB rays as well as common weather elements like snow, rain, and wind. An EPDM rubber roof can endure more than 50 years if properly maintained.
Can EPDM Rubber Roofing Be Painted?
Although the surface of the rubber membrane can be painted, we advise utilising an acrylic finish. Although this paint was created especially for rubber roofing, if you’re still not sure, speak to the EPDM roof’s producer, your installer, or us.
What Is the Cost of Installing An EPDM Roof?
When built properly, EPDM rubber has a lifespan of about 50 years, making it very cost-effective. For a typical 15 m2 single garage, installing rubber roofing will cost between £900 and £1350 (including labour), or between £60 and £90 per m2.
Can A Rubber Roof Be Placed Over Asphalt?
Asphalt can be covered with an EPDM rubber roof, but only if fleece-backed EPDM is used. The roof surface must be flat in order for the rubber membrane to adequately bind to it. On shingles, an EPDM rubber roof cannot be installed.